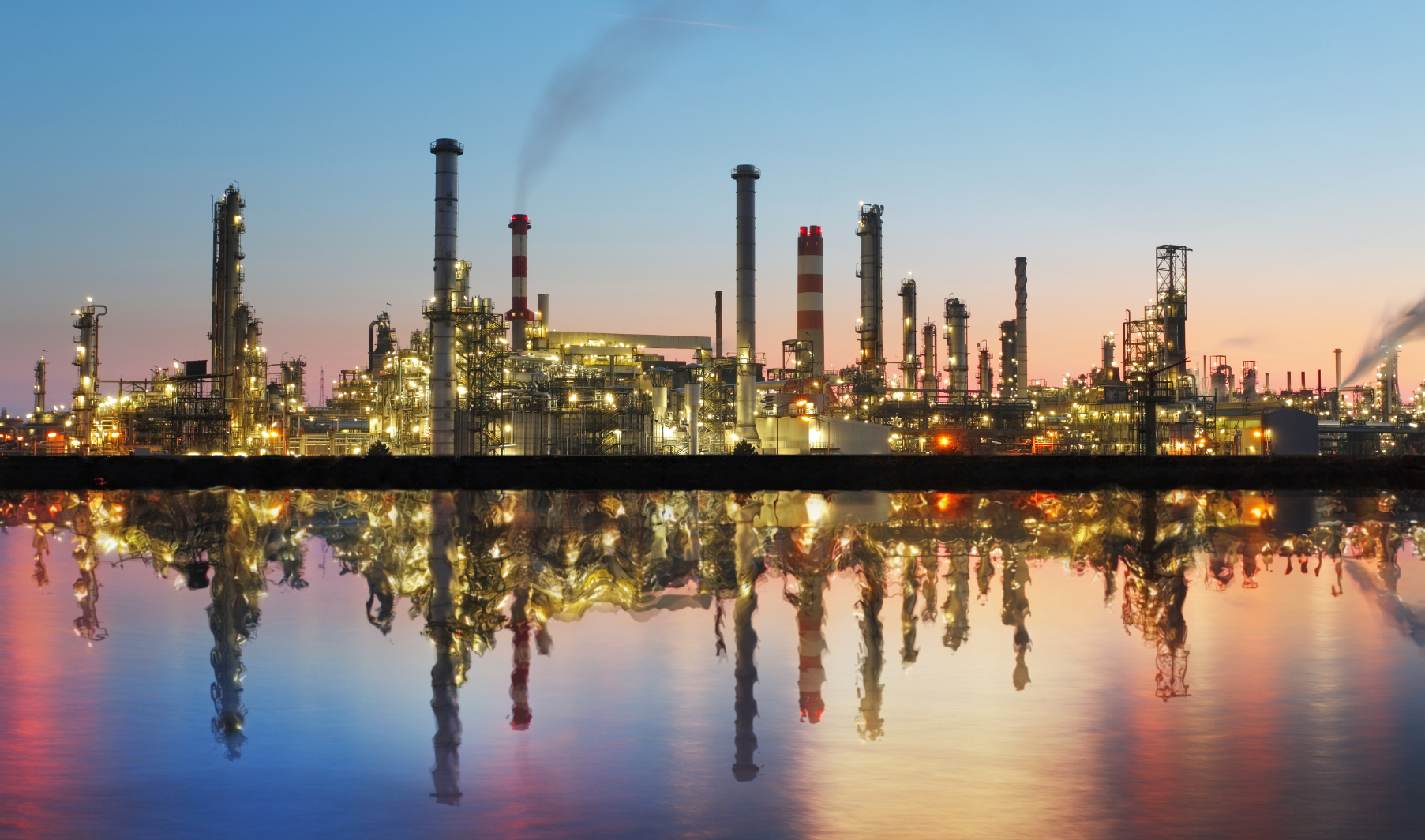
ECO-LOGIC’s proprietary and patented HRT Hydrocarbon Recovery Technology was developed for the total separation of hydrocarbons from a liquid/solid matrix. The HRT technology is energy efficient, provides a low carbon footprint, is environmentally friendly and applicable for OBM/SBM Cuttings, Unconventional Oils (Tar Sands), Tank Bottoms, Oil Sludges, Contaminated Sands & Soils and Natural Asphalt Deposits like on Buton Island in Indonesia.
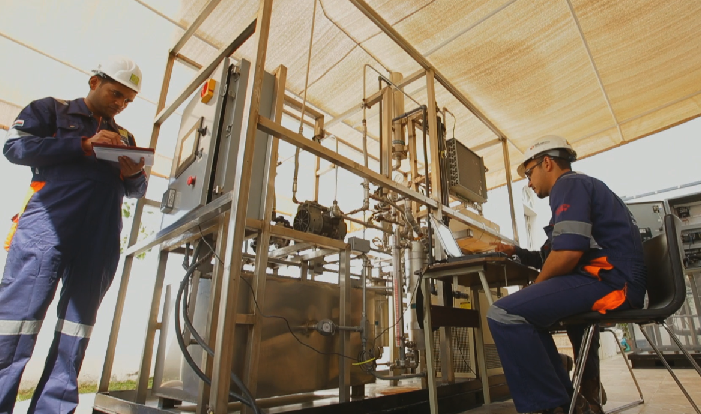
Technology basics:
HRT is based on the physical principle of solvent extraction where the surface interactions between hydrocarbons and matrix are minimized, and the hydrocarbons become diluted in the solvent allowing for emulsion breakdown and a complete separation of the phases.
The product is custom engineered for each application and is based in an azeothropic mixture that is completely non miscible in water via physical activation; so if the waste contains water it will also be separated automatically. The solvent is a proprietary set of compounds (polar protic and aprotic and non-polar), which are designed with very low boiling point temperatures and variable specific gravities that do not interact chemically with hydrocarbons and organic compounds being extracted. The final separation of the product from the hydrocarbons happens through evaporation of the product at a certain temperature and under vacuum conditions, that do not change or negatively affect the hydrocarbons molecular structure. The product is then recovered using a condensing unit on a completely closed system and is reused in the process repeatedly.
The process recovers clean solids, water and clean hydrocarbons and produces no residues or waste streams. The recovered hydrocarbons maintain all their properties due to no chemical interaction with the solvent. The recovered water can undergo conventional water treatment for re-use or responsible discharge.
The technology can be applied in the separation and recovery of complex organic compounds such as crude oils, asphaltenes, paraffins, benzenes, naphthalenes, gasolines, vinyl acetates, diesel, toluene, polychlorinated biphenyls (PCB’s), crude and synthetic oils, etc.
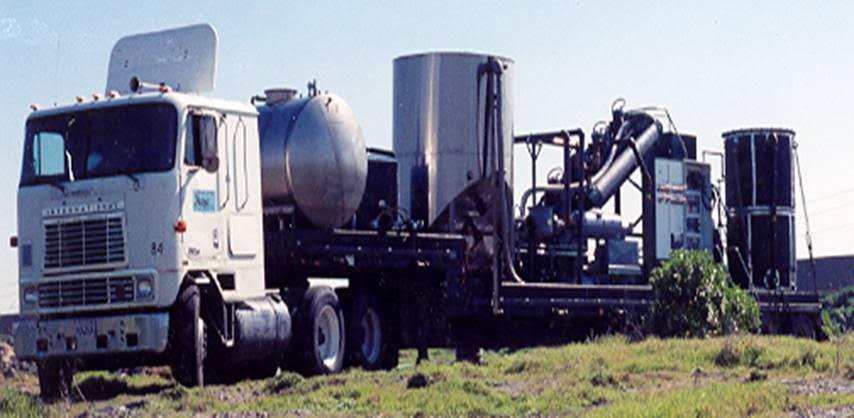
Key facts & features
-
Proprietary solution , patented process and equipment – US2008/0277165 A1
-
Based on Solvent Extraction Processes
-
Using tailored/customized solvents to leach out/extract 99.9% of hydrocarbons present in the feed stream
-
Energy efficient - very low energy consumption, low carbon footprint technology – requiring appr. 10% of the energy of thermal process based units
-
Recapture and reuse of solvents in a closed loop system for maximum efficiency and zero emissions
-
“Process Customized” solvents used, in-house development and production
-
Low temperature processes, 75°C - 90°C
-
Fully automated processes, PLC controlled
-
Closed loop system with high solvent recovery, favorable economics and zero environmental concerns
-
Lower CAPEX than thermal desorption technologies per unit of throughput
-
Mobile, modular plant allows flexibility in deployment – offshore, onshore, in situ, at waste repository
-
Scalable to any required processing rate (MT/hr)
-
Limited human interaction and exposure within the reclamation process, limited HSE exposure & risks
-
Projected processing cost below existing technologies
-
No noxious odors, no HSE exposures
-
Low maintenance schedules, no required/forced shut down periods due to scheduled maintenance – one day per month max (24 hrs operation)
-
Solids : Total Hydrocarbons ≤ 0.1% (1,000ppm)
-
BS&W in recovered oil: ≤1%
-
Oil in Water: ≤40ppm