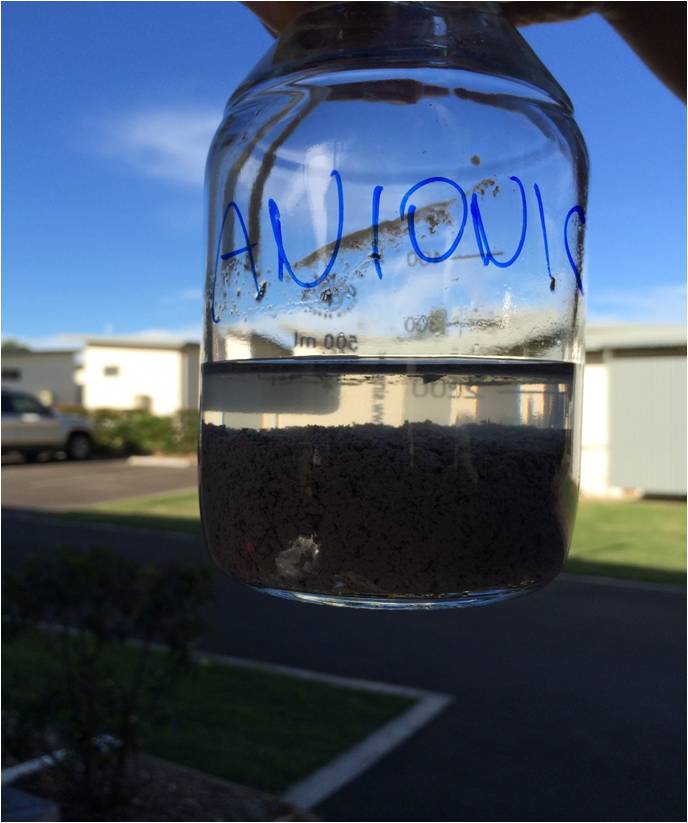
ECO-LOGIC has extensive global experience with wells being drilled with WBM, utilizing the Flocculation/Dewatering Process. The Flocculation/Dewatering process greatly reduces the amount of dilution and eliminates excessive waste volumes normally associated with the “dump and dilute” method. All drilling/completion fluids will be recycled and reused (closed loop), the liquid effluent of the flocculation/dewatering process will either be reused as the base for mixing new drilling fluids, or directly diverted back (controlled and without changing any DF parameters) into the mud system.
ECO-LOGIC provides assistance/technical support on the following, but not limited to:
-
Design of dewatering equipment (dewatering units & centrifuges) – individual, tailor made, application oriented, containerized or open, zone rated if required, onshore & offshore
-
Site/rig surveys – professionally conducted site/rig surveys, survey reports with findings & recommendations
-
Lab & field testing of WBM drilling & completion fluids (selection of most suitable Coagulants and Flocculants)
-
Consumption calculations/estimations, chemical supply and logistics
-
Commercials/budgeting
-
Site/rig setups & layouts – based on site/rig surveys
-
Start up support and execution of projects (if required)
-
Daily and project reporting
-
Specialized manpower recruitment – project management and/or operations personnel
-
Provision of specialized manpower - project management and/or operations personnel
-
Cuttings treatment and disposal – options to responsibly treat and dispose cuttings
Why dewatering? Dewatering benefits:
-
The mechanical liquid solids separation capability of a centrifuge is limited to 6 – 10 microns, depending on centrifuge type
-
Dewatering overcomes this limitation by “flocculating” the feed mud by pre-treating chemically, to increase the “effective particle size” of the suspended solids
-
Effective utilization of the dewatering system can reduce disposal costs by more than 40% - field proven
-
Proven increased overall Solids Control Efficiency of up to 85% - according to API 13
-
Improved mud rheology
-
Improved rate of penetration, ROP
-
Reduced pipe sticking (low solids content)
-
Reduced lost circulation
-
Reduced formation damage
-
Reduced mud costs – elimination of “dump and dilute” to control mud properties/specs
-
Reduced water consumption
-
Ability to achieve stringent discharge compliance
-
Reduced overall well costs $$$$
What is dewatering?
Coagulation and Flocculation
Coagulation and flocculation are processes used to remove suspended and fluid additives from water-based drilling fluids. Finely dispersed solids – colloids – suspended in water are stabilized by negative electric charges on their surfaces, causing them to repel each other. Since this prevents these charged particles from colliding to form larger masses, called flocs, they do not settle. To assist in the removal of colloidal particles from suspension, chemical coagulation and flocculation are required. These processes are a combination of physical and chemical procedures. Chemicals are mixed with water to promote the aggregation of the suspended solids into particles large enough to be settled or be removed.
Coagulation
Coagulation is a chemical process in which the destabilization of colloids takes place. In this process, the forces responsible for keeping the particles apart after they contact, are reduced by coagulant. Coagulation is achieved by neutralizing the particles and thus greatly reducing the repelling forces between the particles. Cationic coagulants provide positive electric charges to reduce the negative charges (zeta potential) of the colloids. As a result, the particles collide to form larger particles (flocs). Rapid mixings required to disperse the coagulant throughout the liquid. Care must be taken not to overdose the coagulants as this can cause a complete charge reversal and re-stabilize the colloid complex.
Flocculation
Flocculation is the action of polymers bringing the destabilized colloidal particles together to form large agglomerates or clumps. Bridging occurs when segments of the polymer chain adsorb on different particles and help particles aggregate. An anionic flocculant will react against a positively charged suspension, adsorbing on the particles and causing destabilization either by bridging or charge neutralization. In this process it is essential that the flocculating agent be added by slow and gentle mixing to allow for contact between the small flocs and to agglomerate them into larger particles. The newly formed agglomerated particles are quite fragile and can be broken apart by shear forces during mixing. Care must also be taken to not overdose the polymer as doing so will cause settling/clarification problems. Anionic polymers themselves are lighter than water. As a result, increasing the dosage will increase the tendency of the floc to float and not settle.
The flocculation reaction not only increases the size of the floc particles to settle them faster, but also affects the physical nature of the floc, making these particles less gelatinous and thereby easier to dewater.
Floc Polymer jar testing
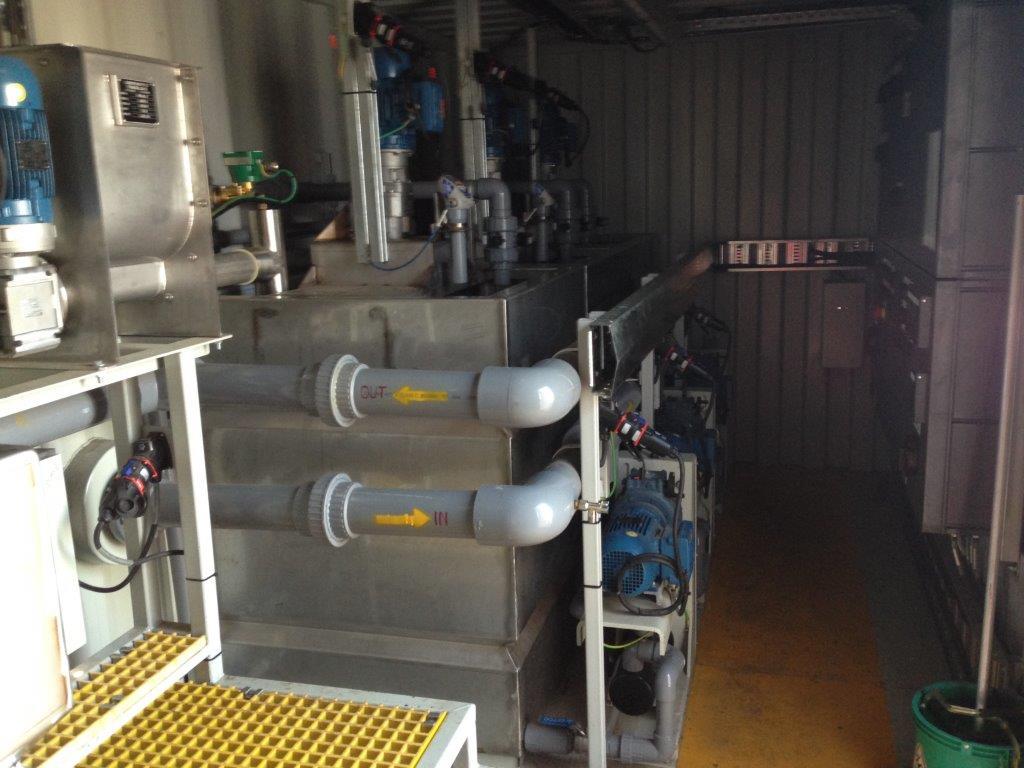
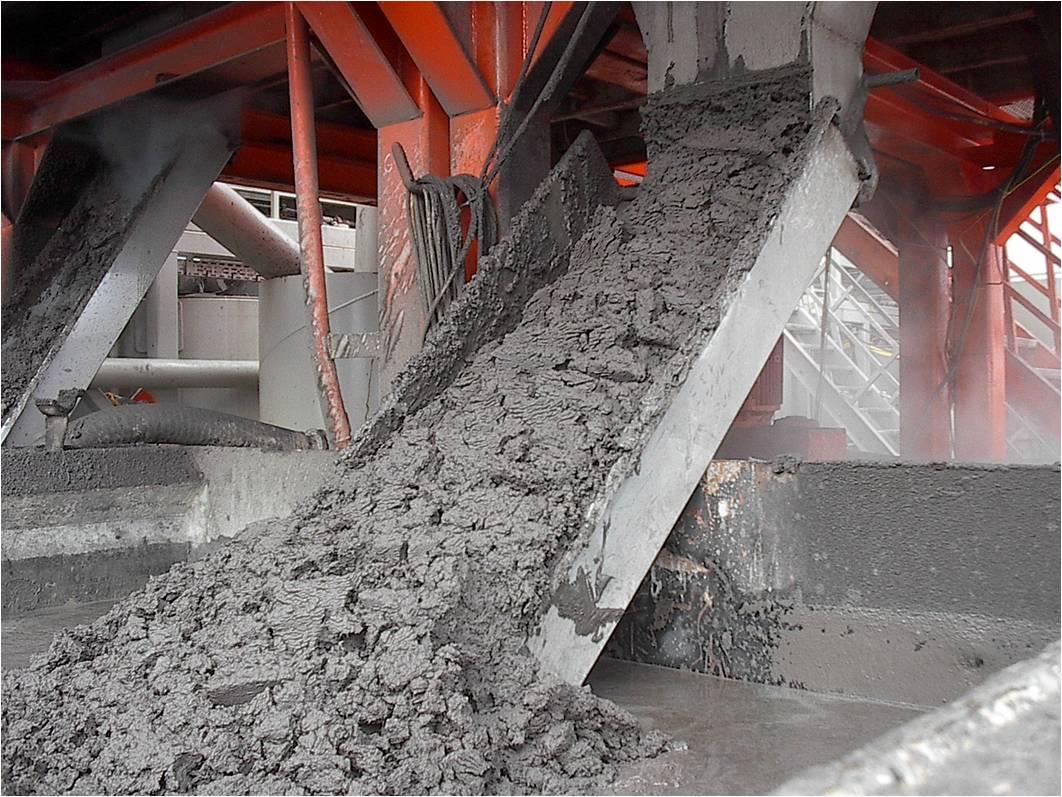